- Category
-
- PVC 7
- Polyolefins 8
- Bioplastics 6
- Synthetic Rubber 9
- Flame retardants 10
- Thermal conductive fillers 1
- Engineering plastics 5
- Paints & Coatings 2
- Plastic Recycling 2
Polyolefins
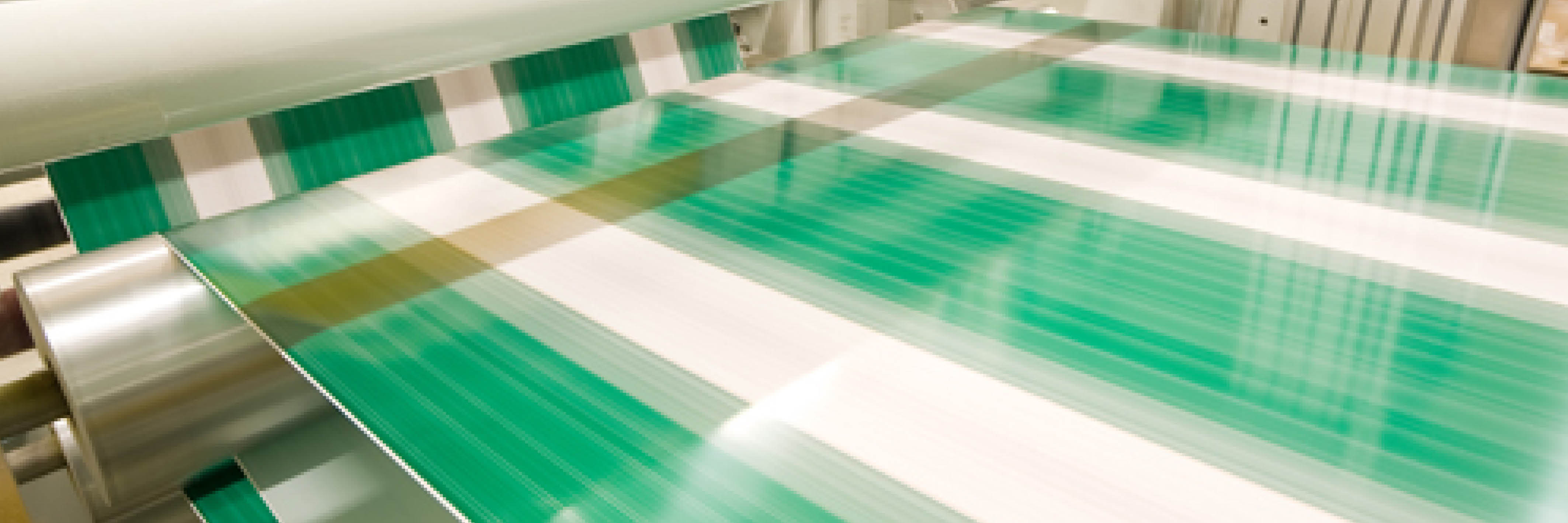
Polyolefins are used in a plethora of applications, including packaging, cable insulation, clothing and medical goods. Before a polyolefin material from the reactor is suitable for its intended application, it needs to undergo several processing steps. The elevated temperatures, shear and exposure to oxygen can cause degradation processes that have a major impact on the polymer melt as well as the mechanical and aesthetic properties of the final article. By selecting the right stabilizing additives, these negatives effects can be largely prevented. The basis of a typical additive package for polyolefins include primary (phenolic-) and secondary antioxidants (phosphites or phosphonites) and acid scavengers. A common acid scavenger used in polyolefins is synthetic hydrotalcite, a material that is being used as stabilizer in polyolefins under the brandname DHT-4A since the late 1970's due to the pioneering work of Kyowa Chemical Industry. The key functionality of hydrotalcites is the irreversible adsorption of acidic catalytic residues. By doing so, hydrotalcites prevent many damaging side effects, most notably corrosion of processing equipment and degradation of the polymer itself. Furthermore, hydrotalcites, and especially high quality materials such as DHT-4A, can synergisticaly improve the performance of other additives and pigments in the formulation. A good example of this effect is the improved performance of Hindered Amine Light Stabilizers (HALS) in the presence of hydrotalcite, resulting in increased weatherability of the polyolefin article.